We are living in an era of fascinating technological advances. Artificial intelligence (AI) is dominating our lives, newly developed engines and power generation devices with fairly high efficiencies make goals once deemed unattainable more reachable than ever.
Today’s electric motors have impressive efficiencies of around 99%. Even with the more traditional engines, such as internal combustion engines, we have reached efficiencies of around 50%. Not long ago, solar panels were deemed expensive, futuristic, and inefficient for generating power. But modern solar cells are being produced much cheaper and with higher efficiencies up to even 40%.
What is next? – Utilizing waste heat.
Even with the current advances and the ones that will come in the next centuries, we will not achieve an efficiency of 100% as we are theoretically bound by thermodynamic laws. Efficiency is defined as the ratio of the useful work done by the system to the total input energy. The second law of thermodynamics states that in any type of energy conversion, some portion of the energy is lost as heat. This is apart from the practical limitations such as material limitations, leakage, and wear, electrical losses, etc., which are being minimized as much as possible by the technology advancements stated above. This energy loss in the form of heat is what we call waste heat.
The common practice for handling this waste heat in the past (and even in the present in various industries in many parts of the world) was to discharge it to the environment e.g., through cooling towers. One could speculate why the term waste heat was used for this portion of the energy, which goes to waste if not used otherwise, i.e., recovered. Hence, we are going to explore the importance of waste heat recovery.
Why recover waste heat?
Recovering waste heat and applying it to other applications is one of the efficient responses to increasing the overall efficiency of the entire energy system (more useful work and less wasted heat). For instance, recovered heat can be used for heating buildings or reused for power generation. But, the benefit of waste heat recovery extends far beyond energy efficiency:
- Reducing Emissions: By capturing waste heat, industries can burn less fuel, directly reducing their carbon footprint.
- Enhancing Energy Security: Every unit of energy recovered reduces the demand for fossil fuels, making economies less dependent on external energy sources.
- A Sustainable Future: Innovations in waste heat recovery could play a vital role in sustainable energy systems. For instance, integrating waste heat with renewable energy sources can help stabilize energy supply and demand.
- Lowering Costs: Recovering waste heat cuts energy bills. For energy-intensive industries, this can translate to millions of dollars in annual savings.
Different waste heat grades
The recovery and applications of the waste heat depend on the grade, which is commonly categorized as follows based on the temperature:
Low-Temperature Waste Heat (Below 200°C)
This heat comes from sources like cooling water in engines or exhaust gases in air conditioners. It’s challenging to use directly because of its low energy density. The common application of this grade of waste heat is to use it directly for heating purposes. Heat pumps are also typically used to increase the temperature to widen the range of possible applications.
Medium-Temperature Waste Heat (200–600°C)
Medium-temperature heat is often found in many industrial processes like cement production or metal forging. Based on the temperature, this heat can be reused for heating purposes or power generation, usually in Organic Rankine cycles (ORC), a technology that works like a steam engine (Rankine cycle) but uses fluids with lower boiling points.
High-Temperature Waste Heat (Above 600°C)
This heat is typically found in power plants or large furnaces. High temperatures make it easier to recover and reuse, often used as the heat source for power generation in gas turbines (Brayton cycle) or creating steam to be used for steam turbines (Rankine cycle).
What are we looking for in FlexRICAN?
One of the research infrastructures (RIs) in the FlexRICAN consortium, European Spallation Source ERIC (ESS), is a cutting-edge research facility designed to generate the world’s most powerful neutron source. Once fully operational, the ESS will provide new possibilities for researchers in material science, medicine, energy, and beyond, putting Europe at the forefront of scientific discoveries.
Research infrastructures like the ESS are energy-intensive by nature. The estimated annual power consumption for the case of ESS is about 175 GWh when operational with a beam power of 2 MW (which is planned to be increased to 5 MW, leading to an annual power consumption of 256 GWh). Figure 1 shows an estimation of the electricity consumption at different parts of ESS and the amount of heat which is expected to be recovered to be used mainly for district heating (The numbers are estimations for the beam power of 2MW).
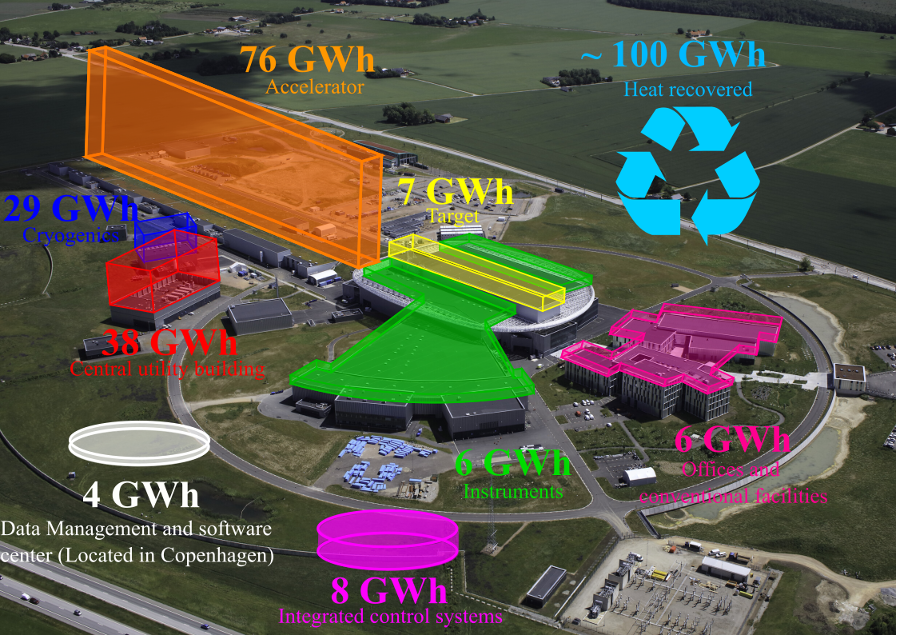
In FlexRICAN, we try to ensure a sustainable approach towards carbon neutrality while keeping this beacon of science up and running. Waste heat recovery is one of the approaches explored within EU funded project – FlexRICAN.
What to do with the waste heat?
At FlexRICAN, we are investigating different approaches to recover and use the waste heat, a process called waste heat valorization. The waste heat generated at ESS falls into the category of low-temperature grade as the temperatures are well below 100°C. This makes the waste heat valorization a bit tricky.
Here are the potential options:
- Local and district heating: A straightforward use of waste heat, particularly for low-temperature waste heat, is to use it for heating. As district heating is the most common way of heating households in Sweden, the infrastructure is already well established. ESS is planned to connect to the district heating network in Lund to transfer its generated waste heat. Furthermore, part of the generated heat will be consumed inside ESS itself.
- Power generation: We can use the waste heat as an input energy for power generation. This could be a bit tricky due to the low-grade waste heat we have and the fact that most power generation cycles need much higher temperatures for the input heat. But there are a few options, such as Organic Rankine Cycles and Stirling Engines, which could work with lower temperatures.
- Absorption/adsorption chillers: Absorption/adsorption chillers are energy-efficient cooling systems that use heat instead of electricity to produce cooling. Absorption chillers rely on a chemical solution, typically water and lithium bromide or ammonia, to absorb heat. A heat source (like waste heat from a power plant or solar energy) drives the process, evaporating the refrigerant and creating cooling in the cycle. Adsorption chillers use a solid material, such as silica gel or activated carbon, to adsorb and release a refrigerant like water or ammonia. Heat causes the refrigerant to evaporate, absorbing heat and producing a cooling effect, just like the human body cooling itself down through perspiration. Both systems are eco-friendly alternatives to conventional air conditioning, especially in settings where waste heat is readily available.
- Transfer the heat to other industries: Many industries could benefit from the heat a research infrastructure such as ESS produces. Especially since many industrial processes require temperatures matching those we have for low-grade waste heat. Potential customers for such waste heat are: Food industry, greenhouses, aquaculture, pulp and paper industry, textile industry, biomass and biogas plants, etc.
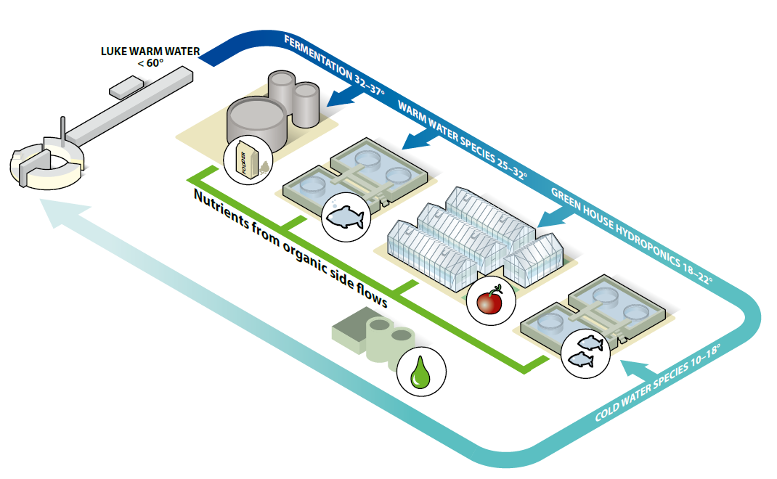
- Thermal storage units: Intermittency could be a big issue when it comes to waste heat Assuming a steady-state operation of the facility, the consumers of the waste heat (mainly the district heating) may not be able to take all the heat energy, especially in warm months. Imagine having a giant rechargeable battery, but instead of electricity, we can store heat energy. This way, we can store the heat and use it whenever it is needed, for example, in colder months.
Waste Heat Recovery is a crucial practice central to potentially driving sustainability. Its adoption can significantly enhance the environmental and operation efficiency of RIs. In the duration of FlexRICAN, the project consortium from 7 countries in Europe will join forces to work on several approaches to offer innovative sustainable solutions, including waste heat recovery, for RIs around Europe to adopt for optimizing their energy use.
To follow the progress and updates, follow our website and social media channels.
Author
This article was written by Peyman Olad, Waste Heat Recovery Research Engineer at European Spallation Source ERIC. Peyman is a Task Leader for two tasks from Work Package 5: Waste Heat Recovery.
References for further reading
[1] V. Pethurajan, S. Sivan, and G. C. Joy, “Issues, comparisons, turbine selections and applications – An overview in organic Rankine cycle,” Energy Conversion and Management, vol. 166, pp. 474–488, Jun. 2018, doi: https://doi.org/10.1016/j.enconman.2018.04.058.
[2] R. Garoby et al., “The European Spallation Source Design,” vol. 93, no. 1, pp. 014001–014001, Dec. 2017, doi: https://doi.org/10.1088/1402-4896/aa9bff.
[3] H. Jouhara, N. Khordehgah, S. Almahmoud, B. Delpech, A. Chauhan, and S. A. Tassou, “Waste heat recovery technologies and applications,” Thermal Science and Engineering Progress, vol. 6, no. 1, pp. 268–289, Jun. 2018, doi: https://doi.org/10.1016/j.tsep.2018.04.017.
[4] Umberto Desideri, “Fundamentals of gas turbine cycles: thermodynamics, efficiency and specific power,” Elsevier eBooks, pp. 44–85, Jan. 2013, doi: https://doi.org/10.1533/9780857096067.1.44.
[5] Guruprasad Alva, Yaxue Lin, and Guiyin Fang, “An overview of thermal energy storage systems,” Energy, vol. 144, pp. 341–378, 2018, doi: https://doi.org/10.1016/j.energy.2017.12.037.
[6] Wei Wu, Baolong Wang, Wenxing Shi, and Xianting Li, “An overview of ammonia-based absorption chillers and heat pumps,” Renewable and Sustainable Energy Reviews, vol. 31, pp. 681–707, 2014, doi: https://doi.org/10.1016/j.rser.2013.12.021.
[7] D.C. Wang, Z.Z. Xia, J.Y. Wu, R.Z. Wang, H. Zhai, and W.D. Dou, “Study of a novel silica gel–water adsorption chiller. Part I. Design and performance prediction,” International Journal of Refrigeration, vol. 28, no. 7, pp. 1073–1083, 2005, doi: https://doi.org/10.1016/j.ijrefrig.2005.03.001.